Comprehending the Basics and Applications of Plastic Extrusion in Modern Manufacturing
In the world of contemporary production, the strategy of plastic extrusion plays a crucial function - plastic extrusion. This intricate process, including the melting and shaping of plastic via specialized dies, is leveraged across numerous sectors for the creation of diverse items. From automobile components to durable goods packaging, the applications are huge, and the possibility for sustainability is just as impressive. Untangling the principles of this procedure reveals the true convenience and possibility of plastic extrusion.
The Principles of Plastic Extrusion Refine
While it may appear complex, the fundamentals of the plastic extrusion process are based on fairly simple principles. It is a manufacturing process wherein plastic is melted and after that formed into a constant profile via a die. The raw plastic product, usually in the form of pellets, is fed right into an extruder. Inside the extruder, the plastic goes through heat and stress, causing it to thaw. The molten plastic is then required via a designed opening, called a die, to create a long, continual product. The extruded product is cooled down and after that reduced to the wanted size. The plastic extrusion procedure is thoroughly utilized in numerous sectors as a result of its versatility, cost-effectiveness, and effectiveness.
Various Types of Plastic Extrusion Methods
Building upon the standard understanding of the plastic extrusion procedure, it is needed to check out the numerous techniques entailed in this production approach. In comparison, sheet extrusion produces big, flat sheets of plastic, which are commonly further processed right into items such as food product packaging, shower drapes, and automobile components. Comprehending these methods is key to making use of plastic extrusion effectively in modern-day production.
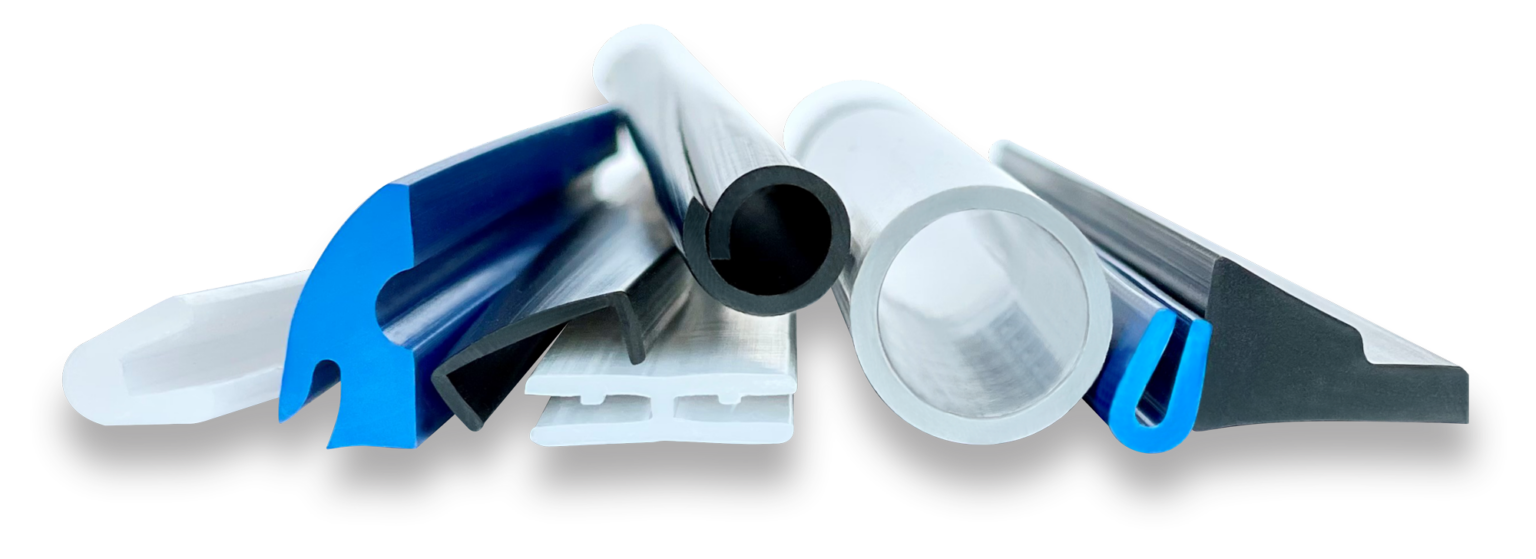
The Function of Plastic Extrusion in the Automotive Industry
An overwhelming bulk of components in contemporary vehicles are items of the plastic extrusion process. Plastic extrusion is largely made use of in the production of different car elements such as bumpers, grills, door panels, and control panel trim. Thus, plastic extrusion plays an essential duty in automobile manufacturing.
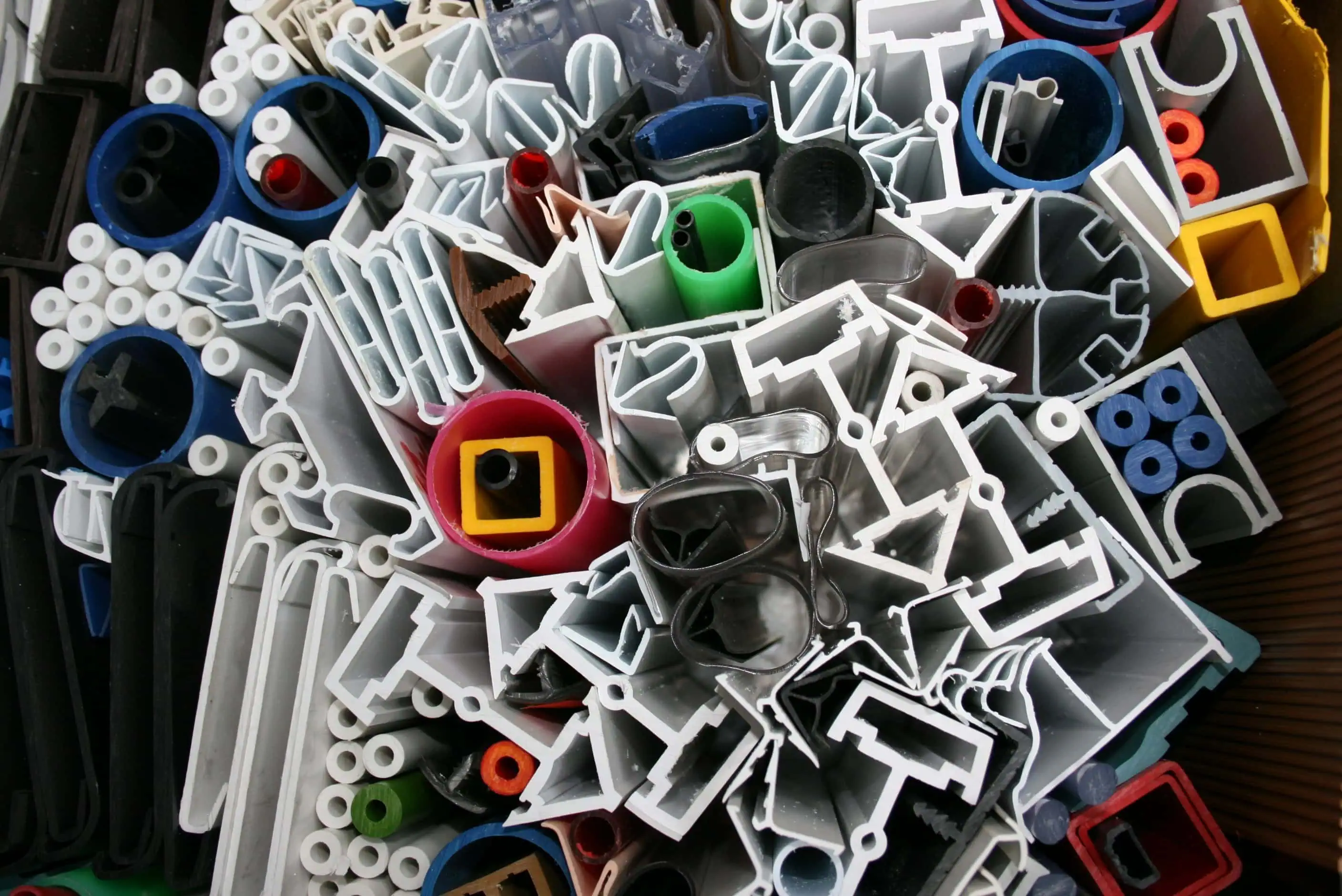
Applications of Plastic Extrusion in Customer Item Manufacturing
Past its substantial influence on the auto industry, plastic extrusion proves equally effective in the realm of customer goods manufacturing. This process is important in developing a broad array of products, from food product packaging to house devices, playthings, and even medical devices. The adaptability of plastic extrusion permits manufacturers to develop and generate intricate sizes and shapes with high precision and performance. Additionally, because of the recyclability of several plastics, squeezed out elements can be reprocessed, minimizing waste and i was reading this price. The adaptability, adaptability, and cost-effectiveness of plastic extrusion make it a favored option for numerous customer goods makers, adding dramatically to the industry's growth and technology. The environmental ramifications of this extensive use call for cautious consideration, a subject to be talked about better in the succeeding area.
Ecological Effect and Sustainability in Plastic Extrusion
The prevalent usage of Home Page plastic extrusion in producing welcomes examination of its environmental effects. Effective machinery lowers power usage, while waste monitoring systems reuse scrap plastic, lowering raw product demands. Despite these renovations, additionally advancement is needed to mitigate the ecological footprint of plastic extrusion.
Conclusion
To conclude, plastic extrusion plays an essential duty in modern-day manufacturing, especially in the automotive and consumer goods industries. Its adaptability enables the manufacturing of a wide variety of parts with high precision. In addition, its capacity for reusing and advancement of naturally degradable materials provides an appealing opportunity in the direction of sustainable methods, thus dealing with ecological worries. Comprehending the basics of this procedure is key to enhancing its benefits and applications.
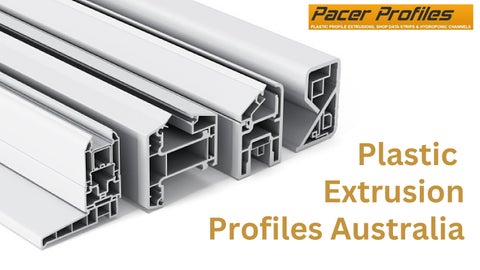
The plastic extrusion process is thoroughly used in different sectors due to its versatility, cost-effectiveness, and efficiency.
Building upon the basic understanding of the plastic extrusion process, it is necessary to discover the different methods included in this production technique. plastic extrusion. In contrast, sheet extrusion produces huge, level sheets of plastic, which are typically additional processed right into products such as food packaging, shower drapes, and cars and truck parts.A frustrating bulk of components in modern-day cars are items of click to investigate the plastic extrusion procedure
Comments on “Custom plastic extrusion tailored to your industry needs”